Summary:
UCLA researchers in the Department of Mechanical and Aerospace Engineering have designed a modular robotic system termed the Latching Intelligent Modular Mobility System (LIMMS) for the manipulation of a typical last-mile delivery.
TITLE: Latching Intelligent Modular Mobility System (LIMMS) for Logistics and Last-Mile Delivery
Background:
The rapid growth of e-commerce has placed tremendous pressure on companies to efficiently deliver packages directly to customers' homes, transforming the delivery landscape and making last-mile logistics a critical focus for businesses. While last-mile delivery is crucial to the overall customer experience, the process is complicated by the range in urban terrains and package size and weight. Traditional methods of last-mile delivery rely heavily on manual labor, which is costly and time-consuming. Recent advances in wheeled and legged robotic delivery systems have addressed some of these issues. The design complexities posed by dynamic environments and varying package sizes, however, have hindered the effectiveness of existing robotic platforms. Additionally, these technologies tend to occupy a large amount space and have a high cost of transport, limiting their use in general purpose deliveries. There remains a need for an affordable and automated robotic system that can efficiently deliver a large number of packages and traverse a range of unpredictable environments for last-mile deliveries.
Innovation:
UCLA researchers in the Department of Mechanical and Aerospace Engineering have developed a modular robotic system, the Latching Intelligent Modular Mobility System (LIMMS), specifically tailored to address the challenges of last-mile delivery. The design removes the need for a centralized body by using the package being transported or the inside walls of the delivery vehicle for that purpose. Limb-like robots equipped with latching mechanisms are attached to the vehicle wall or payload. This modular approach offers significant energy and space savings in delivery tasks. The latching mechanisms allow for a significant tolerance to misalignment that is twice as high as traditional methods (2X). Furthermore, LIMMS exhibits remarkable versatility, enabling it to perform a wide range of tasks by skillfully interacting with the surroundings and adeptly manipulating objects. In a typical delivery scenario, LIMMS units attach themselves to anchor points within delivery trucks, providing assistance in the movement of boxes. Once the package is positioned for removal from the vehicle, the LIMMS units attach to the box, transforming into a quadruped structure that facilitates autonomous delivery. LIMMS units are engineered to operate effectively within dynamic environments and have the capacity to handle diverse package sizes and loads, ensuring optimal performance and adaptability. Furthermore, the design principles underlying LIMMS have the potential for broader applications beyond last-mile delivery. For instance, the device can be adapted to develop innovative robotic systems aimed at safely transporting wounded soldiers from the battlefield to secure zones. The first hardware prototype of this system has been successfully designed and demonstrated.
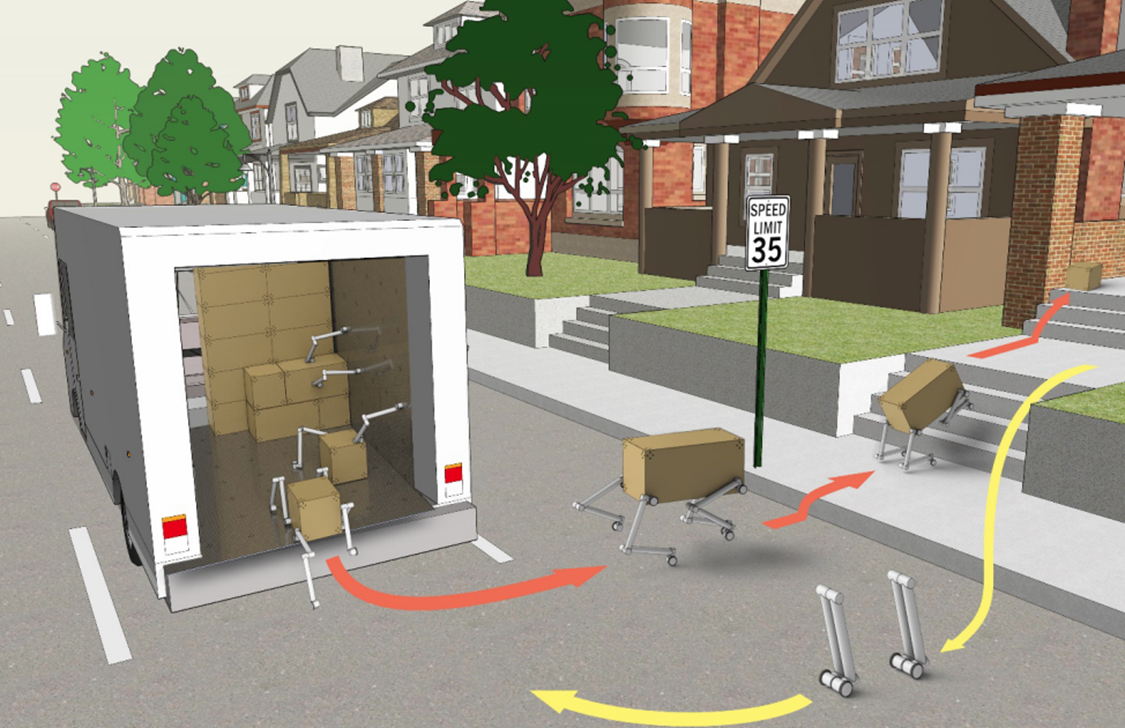
Schematic of the LIMMS device. Credit: Dr. Dennis Hong
Potential Applications:
• Robots for automated last-mile delivery
• Robots to move equipment/materials inside humanless warehouse/factory
• Autonomous robots that can carry wounded soldiers to safety
• Other mechanical systems that require similar latching mechanisms
Advantages:
• Great mobility and manipulation capability
• Robust and compact design
• Saves energy and space
• Adapts to different environment based on need
• Tolerates a high degree of misalignment
• Highly customizable
Development to Date:
First successful demonstration of the invention: September 2021
Related Papers:
Zhu, Taoyuanmin, Gabriel I. Fernandez, Colin Togashi, Yeting Liu, and Dennis Hong. "Feasibility study of limms, a multi-agent modular robotic delivery system with various locomotion and manipulation modes." In 2022 19th International Conference on Ubiquitous Robots (UR), pp. 30-37. IEEE, 2022.
Fernandez, Gabriel I., Samuel Gessow, Justin Quan, and Dennis Hong. "Self-aligning rotational latching mechanisms." In International Design Engineering Technical Conferences and Computers and Information in Engineering Conference, vol. 86281, p. V007T07A024. American Society of Mechanical Engineers, 2022.
Reference: UCLA Case No. 2023-170 and 2023-171
Lead Inventor: =Taoyuanmin Zhu (2023-170); Gabriel Ikaika Fernandez (2023-171); Prof. Dennis Hong (both).