Summary:
Researchers in the Mechanical Engineering Department at UCLA have developed a compliant technique that can be utilized for a wide array of industries, including next-generation joint reconstruction surgeries, precision manufacturing, robotics, aerospace transportation, and automation applications.
Background:
Bearings are commonly used to reduce friction and improve movement between moving parts in large mechanical systems. Conventional mechanical bearings, such as sliding and rolling bearings, have been developed to withstand large mechanical loads while decreasing friction. This allows for a longer lifespan of the components and higher efficiency. Joint reconstruction surgeries are one prominent application requiring mechanical bearings, which allow implanted metal components to have natural movement characteristics and reduce wear and tear for highly active patients. However, these types of bearings are not frictionless and typically will have limits on their efficiency. Therefore, flexure bearings may provide a suitable alternative to these bearings. Flexure bearings enable frictionless motion using compliant flexures rather than sliding or rolling contacts, and are highly efficient, wear-resistant, and provide repeatable motion for applications requiring high precision. However, their load capacity is inherently limited by their range of motion, restricting their broader adoption in systems requiring occasional extended motion ranges. Conventional bearings, while capable of handling larger loads and extended ranges, introduce friction, wear, and maintenance demands. This trade-off between efficiency and versatility has driven the need for a new solution to address these limitations to improve long-term durability, flexibility, and range of motion for bearings in a variety of industries.
Innovation:
UCLA researchers in the department of Mechanical Engineering have developed a metamorphic flexure bearing that operates in two distinct modes: a flexure-bearing mode for regular use, preserving its efficiency and low wear, and a conventional-bearing mode for intermittent extended motion, accommodating higher loads at the expense of increased friction. The dynamic nature of this metamorphic bearing allows it to automatically transition between conventional and flexure bearing types to accommodate specific ranges of motion. This innovation merges the advantages of both bearing types, creating a versatile solution for mechanisms such as automotive steering and aviation controls. These systems primarily require precise, small-range motion but occasionally necessitate extended movement. By redefining traditional mechanical bearings, this design enhances performance across various applications, including joint reconstruction, medical implants, robotics, and aerospace engineering.
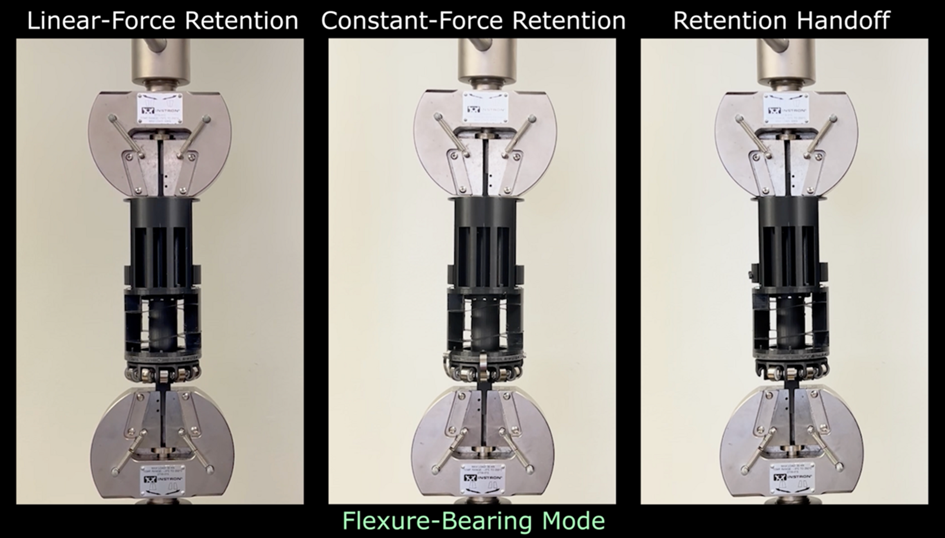
Source: 10.36227/techrxiv.172954209.92752104/v1
Potential Applications:
• Orthopaedic Joint Reconstruction
• High precision applications, pick-and-place machines or 3D-printers
• Medical devices such as surgical tools or exoskeletons
• Robotics and automation
• Automative Systems (steering mechanisms, suspension systems)
• Aerospace and Aviation (control yokes and joysticks, landing gear mechanisms)
• Industrial machinery precision tools and actuators
Advantages:
• Dual-mode functionality of flexure-bearing and conventional-bearing modes
• Extended range of motion
• Increased load capacity
• Increased wear-resistant
• High efficiency, low maintenance and improved longevity due to frictionless operation
• Customizability to specific load profiles and applications
• Increased versatility in applications
State of Development:
This invention was first conceived in early September 2023 and the first description of the complete invention was in April of 2024. A peer-reviewed paper is under submission and a draft can be found here: 10.36227/techrxiv.172954209.92752104/v1. Application of this technology to orthopaedic implants is still in the early conceptual stages. Prior to commercial viability, any implant architecture that incorporates this technology will need to be reduced to a viable product, evaluated pre-clinically for safety and efficacy, and then validated in early clinical trials under an IDE (not yet submitted to the FDA).
Related Papers:
1. Cameron Taylor, Will Flanagan, et. Al. (2024) “Metamorphic Flexure Bearigns for Extended Range of Motion” TechRxiv. October 21, 2024. 10.36227/techrxiv.172954209.92752104/v1
2. Hongzhe Zhao, Shusheng Bi and Jingjun Yu. (2012). "A novel compliant linear-motion mechanism based on parasitic motion compensation" Mechanism and Machine Theory. 50 (15-28), ISSN 0094-114X; https://doi.org/10.1016/j.mechmachtheory.2011.11.009.
Reference:
UCLA Case No. 2025-038